Designing and delivering factories for green technologies (such as hydrogen) is one of the great challenges of the net-zero transition, as cost overruns and extended timelines for capital projects are common. According to senior partner Zak Cutler and colleague, industrializing the end-to-end process of completing big factory projects, also known as the plant-as-a-product approach, can lower capital expenditure costs by as much as 75 percent over time. A reduction in capital expenditures for batteries and solar and wind technologies shows that scaling the green tech of the future is tough but within reach.
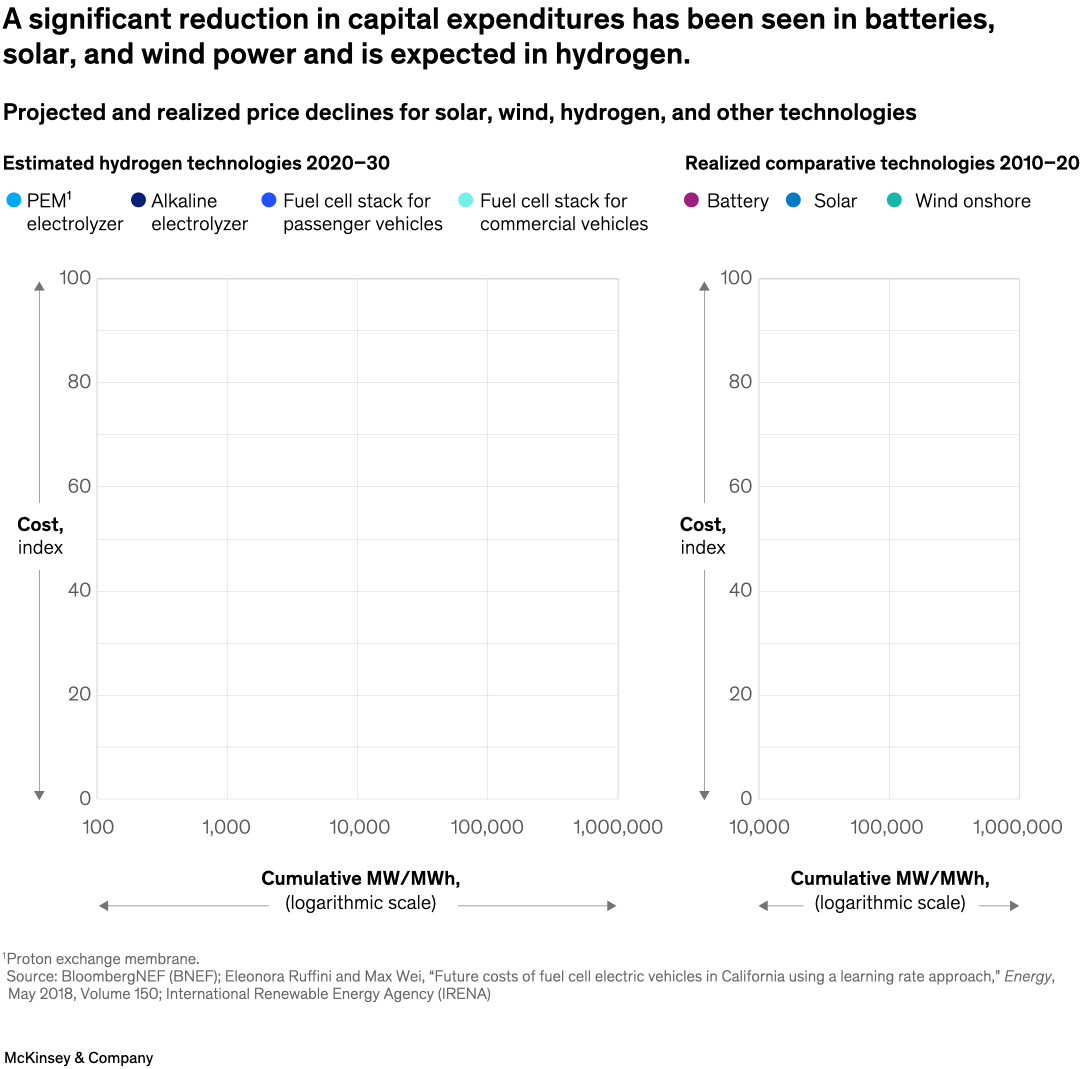
Image description:
A line graph shows the estimated cost declines of different hydrogen technologies, where the y-axis represents a cost index of 0 to 100 and the x-axis represents a logarithmic scale of the cumulative megawatts (MW) per megawatt-hour (MWh) for each technology. The lines show the more MWs a hydrogen technology produces, the lower its potential cost. Hydrogen technologies include proton exchange membrane electrolyzer, alkaline electrolyzer, fuel cell stack for passenger vehicles, and fuel cell stack for commercial vehicles. In comparison, another line graph shows the realized cost declines of battery, solar, and wind onshore, which fell in cost as their production increased.
Source: BloombergNEF; Eleonora Ruffini and Max Wei, “Future costs of fuel cell electric vehicles in California using a learning rate approach,” Energy, May 2018, Volume 150;
International Renewable Energy Agency.
End of image description.
To read the article, see “The plant as a product: Hyperscaling green capex,” September 7, 2023.